Enhance
See how we developed a solution to accurately measure an athlete's performance.

The primary challenge was to develop a reliable and precise testing mechanism.
Introduction
Our client presented us with a unique challenge involving the need for an instrument designed to replicate the motion dynamics of running. An “Exoskeleton” device attaches to a user’s calf and shoe and is engineered to assist in driving the user’s ankle downward during running. This enhances performance and helps a runner train for improved form. The client required our expertise in creating a test fixture to quantitatively assess the performance of the Exoskeleton.
Problem Statement
The primary challenge was to develop a reliable and precise testing mechanism that could accurately measure the performance enhancements offered by the Exoskeleton. This required a solution that could not only replicate the motion dynamics of running but also capture detailed data on the torque and force exerted by the Exoskeleton during operation and its angular position.
Solution
To address this challenge, we engineered a test fixture utilizing a servo motor. This motor essentially “moves the ground” while the “foot” is free to rotate, mimicking a runner's step. We collected the torque along the shaft from the motor, the force at the sole, and the angular position of the motor. We used a National Instruments Data Acquisition device for data collection which was then forwarded to a laptop to run custom software for data analysis. Finally, we used a Raspberry PI to interface with the Exoskeleton to collect the torque and ankle position from the Exoskeleton’s internal sensors and sent that information to the laptop as well.

Here’s How We Solved It
System Integration: We focused on achieving precise control over the motor movements and effective data collection from the NI cDAQ-9185 (DAQ). This involved integrating the ADM32E Servo Motor for dynamic movement of the Exoskeleton and ensuring that the torque transducer, force transducer, and encoder were accurately relaying data to the DAQ. Our team tested the system to ensure that the motor commands and data acquisition processes were optimized for accuracy and timing, essential for evaluating the Exoskeleton's performance. Mechanical Design: The project aimed to approximate a simulation of a human running. To achieve this, we fastened a shoe onto a synthetic foot, which was mounted on a mechanical appendage. The appendage, featuring a spring mechanism, was designed to approximate the weight of a user so that the force is only applied when the foot contacts the “ground.” This structure was key in approximating the motions and forces generated by the Exoskeleton during a run. We designed the spring so it could be moved to several positions to simulate different body weights.
Data Acquisition and Analysis: The torque transducer, force transducer, and encoder were used in capturing torque, force, and angular data. This data streamed into the DAQ, linked to a laptop. Here, the data was cleaned up, converted to proper units, visualized in graphs, and exported as a CSV file through a custom windows application written in C#, facilitating in-depth analysis.
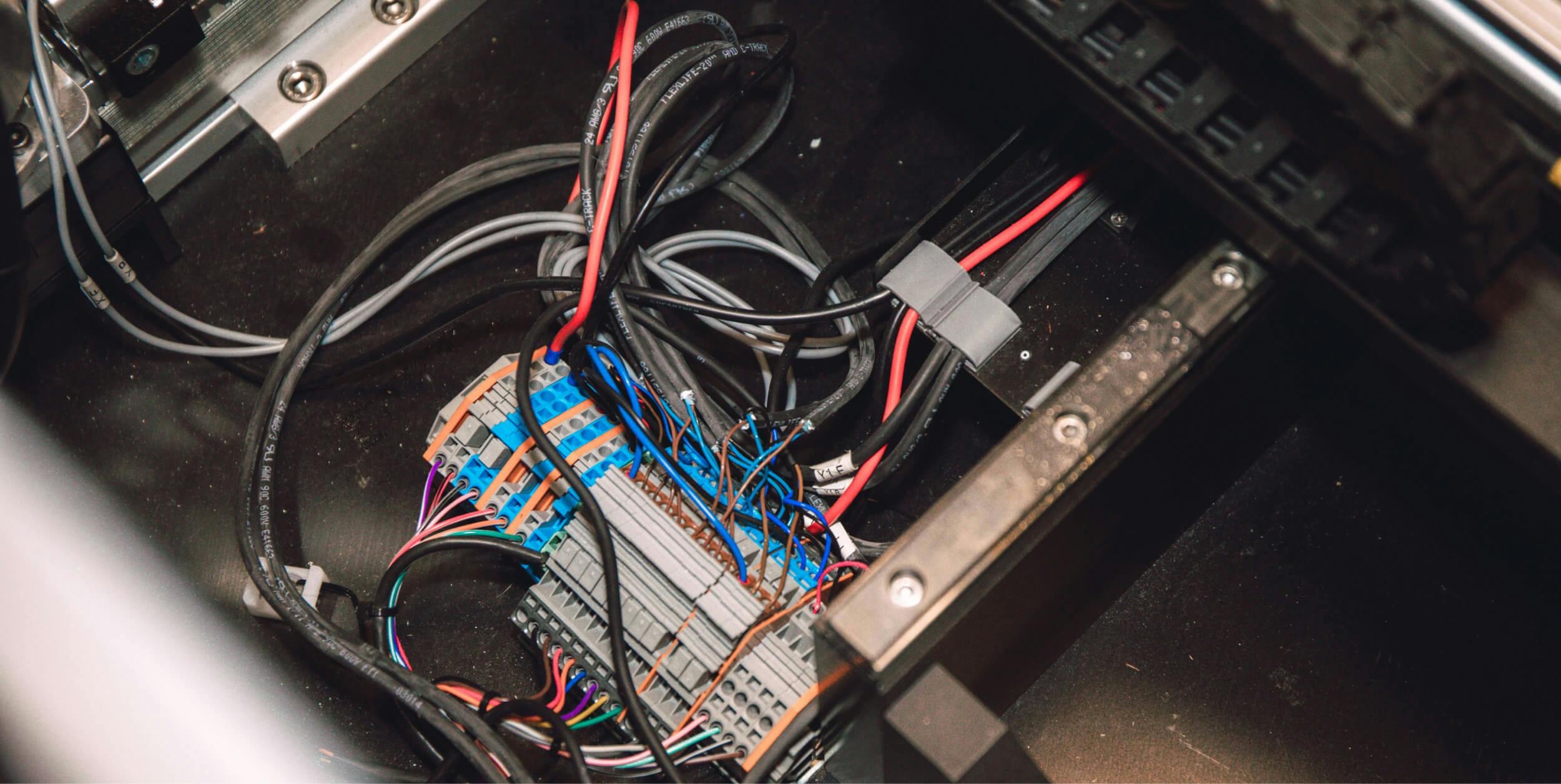