Advances in 3D Printing

3D Printing isn’t new, but recent emerging technologies present exciting new developments that will transform the industry. Additive Manufacturing, commonly referred to as 3D Printing, is the printing of objects – building layer upon layer under automated control, starting with a virtual 3D model and ending with a dimensionally representative physical part. 3D printing has been used for decades by architects, designers and engineers as a way to quickly prototype parts to evaluate aesthetics, fit and function. Over the past few years we’ve seen a surge in publicity about 3D printing, touting the advent of personal at-home printers, medical applications, and food printers. Reviewing where this technology has been and where it is going gives us an indication of the incredible advances being made today. Advances in 3D printing will affect businesses and how they work as well as how consumers obtain needed products.
HISTORY
3D printing was first demonstrated in the 1970’s and was established in the 1980’s with the stereolithography (SLA) process patented in 1983 and the introduction of the stereolithography (STL) file format used to convert 3D CAD files into sliced layers that are printed to form a volume. Selective Laser Sintering (SLS) machines were patented in 1986, and Fused Deposition Modeling (FDM) was patented in 1988. The first commercially viable SLA printer was introduced in 1988, and 3D printed prototype parts, although expensive, became widely available in the 1990’s. 3D printing innovation continued with commercially available color 3D printing in 1996, while RepRap (2005) and Thingverse / MakerBot (2008) sought to bring open-source 3D printing to the masses.
USES
More recently, 3D printing innovations are advancing the use of existing technology as opposed to inventing new methods of printing as seen with the first 3D printed car, 3D printed chocolate, and a 3D printed model airplane. In 2013 and 2014, the news media regularly reported amazing advancements like a 3-D printed house, doctors using a 3D printed splint to help a baby breathe, 3D printed clothes and 3D printed shapes made from sugar.
Prototypes
3D printing continues to be used by engineers and design houses for rapid prototyping of parts. Due to advancements in speed, cost, and size of 3D printers, in-house 3D printing is now a possibility for many businesses and using 3D printing houses is more affordable.
This part demonstrates a simple 3D printed part assembled with non-3D printed parts to quickly evaluate fit and function.
Finished Parts
With current technology, it is now cost-effective to 3D print unique and costly items for end use, like dental devices, hearing aids, and jewelry.
Custom Printing
Nike, Adidas, and Under Armour have produced limited-edition custom shoes and cleats for elite athletes, and in April 2016 New Balance offered a limited-edition running shoe for sale with a 3-D printed midsole. There is also a whole market segment of 3D printing specializing in custom 3-D printed figurines, featuring several ways that you can 3-D print figurines of yourself based on photographs or 3D scans.
INNOVATIONS
Technology Advancements
Larger 3D Printer manufacturers like 3D systems and Stratasys are investing engineering effort into producing more cost-effective, reliable, easy-to-use 3D printers that make more accurate parts with a greater range of materials.
HP just introduced a new 3D printer using their recently patented Multi-Jet Fusion (MJF) technology, which promises 3D printed parts with improved “strength, accuracy, resiliency and finish” that print 10 times faster and deliver superior parts at less than half the costs of competitors.
Technology advancements were on display at RAPID 2016, the preeminent event for 3D printing, scanning, and additive manufacturing. Members from SIGMADESIGN attended the conference in Orlando on May 16-19, 2016. Ben Mergen, a SIGMADESIGN Mechanical Engineer at the show, watched the demonstration of HP’s MJF technology with a peek at future printer models. These new models integrate sensors directly into a printed object so it can report in real time the stresses placed on it.
Mergen remarks, “The most innovative application for 3DP that I saw was Hoosier Pattern (www.hoosierpattern.com).” Hoosier uses sand as a medium to 3D print sand casting molds. With most 3DP technologies, the part produced comes out very close to the desired part, but it’s usually not quite perfect. Mergen comments, “What’s brilliant about Hoosier Pattern’s niche is: a casting is a casting, regardless of how you make the mold. Basically, they found an application that leverages all the benefits of 3D printing while also making most of the drawbacks irrelevant. Pretty cool!” Read more about RAPID and insights from Ben.
Consumer Printer Advancements
Expiring patents have paved the way for enterprising companies to create a new generation of affordable FDM and SLA printers for small business or personal use, and we anticipate a similar adoption of the recently expired SLS patent. But a word of warning – as many hobbyists are finding, to make functional, reliable parts there is a fair amount of effort required to turn CAD files into STL files and then into 3D printed parts that meet the need of the application. With a wider range of materials available in multiple technologies, engineering knowledge becomes more critical with regards to determining the optimal geometry for the application, material properties, and internal support structure, all of which contribute to the part strength, fit, and durability.
Application Advancements
3D printed metal is a particularly compelling concept. The ability to print metal into a complex shape without the waste incurred with traditional machining methods and without the casting molds or post-processing required with cast parts opens up a new world of possibilities. Multiple 3D printer manufacturers are producing metal 3D printers using Selective Laser Melting (SLM) and Direct Metal Laser Sintering (DMLS), allowing thinner walls, tighter tolerances, and larger prints.
Designing a multi-part assembly can be one of the more challenging and tedious aspects of preparing parts to be released for production, particularly for high quantity production. The ability to 3D print an assembly as one part eliminates much of the tedious work and allows the engineering effort to focus on the function of the part. A good example of this is GE’s 3D printed fuel injection system for their LEAP engine. Not only were 18 parts combined into one complex 3D printed part, the 3D printed part is 25% lighter in weight than the assembly it replaces. 3D printing allows more intricate cooling paths that result in a 5X increase in durability over conventionally manufactured parts and an increase in fuel efficiency.
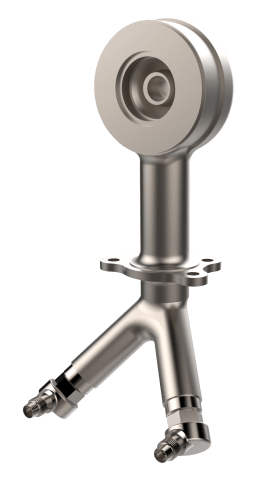
SIGMADESIGN RENDERED THIS EXAMPLE PART WHICH PORTRAYS GE’S 3D-PRINTED FUEL INJECTION SYSTEM. IN THIS EXAMPLE, THE PIECE WENT FROM AN 18-PART ASSEMBLY TO 1 COMPLEX 3D -PRINTED PART. (READ MORE ABOUT GE AND THIS PART).
It’s fascinating to think of the barriers 3D printing removes and the complex geometry that can now be printed. Artificial Intelligence optimizing algorithms can produce CAD designs optimized for fluid flow or cooling that can only be made on a 3D printer. Complex, moving assemblies like gear trains can be printed as one 3D printed system, tightly controlling the relative placements with the tolerance inherent to the 3D printer instead of the part-to-part assembly tolerance. Plastic parts can also be printed with multiple durometers in one part. Multi-Jet Printing (MJP) technology allows printing hard and soft plastics; it “simultaneously prints and fuses together flexible and rigid material composites, layer-by-layer at the pixel level.” Hard next to soft material or hard mixed with soft in a gradient means we can now create single parts with complex functionality.
Another example (rendering by SIGMADESIGN) shows a multi-material 3D-printed industrial part. Printing multi-material parts like this are possible with the ProJet 5500X (Read more about 3D Systems).
Future
On-demand printing in the manufacturing setting means not having to stock inventory; rather, you print what is needed when it is needed, exchanging physical inventory for virtual inventory. The idea is that all parts needed in an assembly would live in “virtual inventory” as an STL file. When the part is needed for assembly, the STL file is sent to the printer capable of printing the part in the needed material. This means 3D printers have to be fast enough, cost-effective enough, and reliable enough to compete with current part production methods. There are indications that this transition to accessible 3D printers is happening. US manufacturers in 2016 report increased usage of 3D printed parts, with more than half of manufacturers reporting using 3D printing for prototyping or printing final parts, compared to 35% two years ago. In a small-scale demonstration of on-demand part production, NASA is currently experimenting with a small FDM-style 3D printer on the international space station. NASA will send STL files of parts required for maintenance, and those parts are then printed out on the space station only when they are needed.
Medical Applications
Custom knee replacements based on CT scans are now a reality, as well as 3D printed models from CT scans that surgeons use to plan joint replacement surgeries. Ongoing research in medical applications include bio-printing organs for organ replacements, and bio-printing cartilage and joint replacements based on an scan of the person’s own joint.
Impacts to Industry
3D Printing technology has made incredible advances lately and more are inevitable. These advances will change how many of us do business today. Some of these factors are listed below:
Sector | Change | Benefits |
Research & Development | Able to print larger, more complex parts out of multiple materials | Innovative functionality, taking advantage of decreased limitations. |
Design & Engineering | Cost-effective, reliable 3D printing | Removes prototyping constraints. 3D printing replaces engineering model shops? |
Manufacturing | Virtual Inventory | Manufacture parts on-demand, reduce money tied up in inventory |
Medical | Bio-printing organs, joint replacements | Improve or save a human life |
Consumer | Access to technologies other than FDM (SLA, SLS) | Ability to make dimensionally accurate parts from a wider range of materials at a much lower cost |
Many changes are on the horizon. With the innovations in 3D printing. consumer and industrial goods become more localized. Industry will see the most dramatic changes and 3D printing factories will become connected in a global production network. For consumers, the ability to create complex parts on demand creates a world of customization. Everything we know can be made closer to us.