By Daniel Stuart, Systems Control Engineer

Systems Engineers bring value to the product design process by working with clients to understand the product requirements and then facilitating concept exploration and evaluation in order to select an optimal product. Clients come to Sigma Design with a product idea or process challenge that will create/meet a market need or address a production opportunity. The client may need help with designing a new product, correcting an existing product, developing a new process, or correcting a process that isn’t working properly. Frequently, clients know what a successful product will be able to do, but are not always sure how to accomplish the various aspects of their objective. This is when enlisting a good systems engineer will prove very valuable.
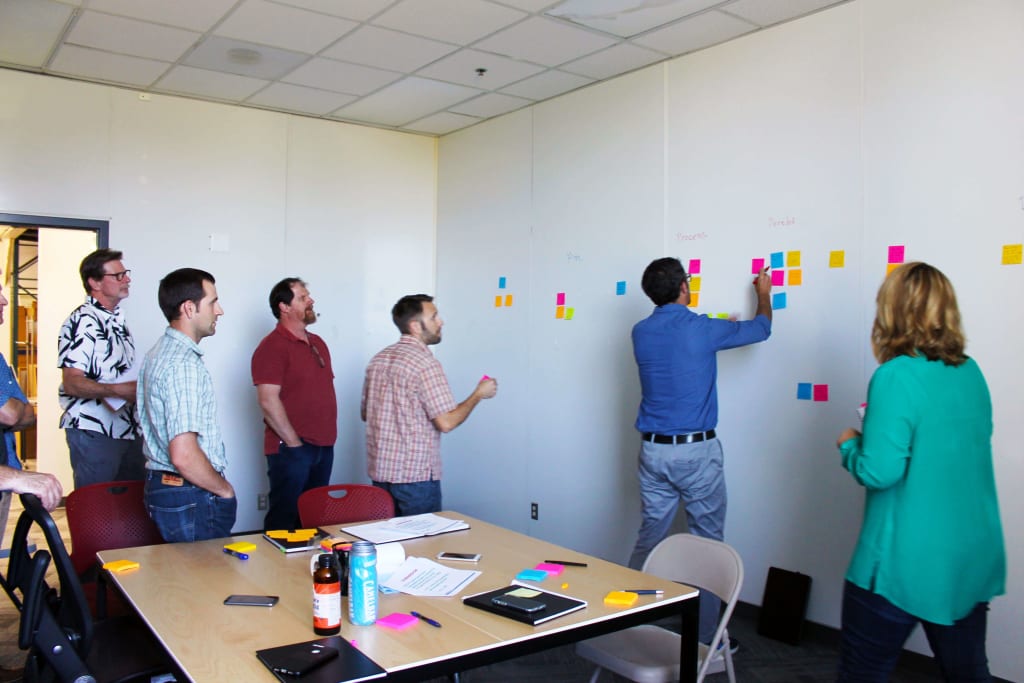

To begin, a Systems Engineer works with experts in relevant product development disciplines (ID, ME, EE, FW, SW, etc.) to brainstorm multiple concepts that meet the high level product or process requirements. Each of the concepts are then fleshed out to understand feasibility. Mechanisms are explored in CAD, systems are numerically modeled, and potential key components are evaluated for cost and performance. Where appropriate, concepts are evaluated using Pugh matrix techniques to assess the pros and cons of each concept against a variety of metrics (quality, cost, and delivery) at the same time. This is where the process of down selecting to the final concept begins. The Pugh analysis provides valuable structure to the down select process.
Concept exploration and evaluation proves especially valuable for large projects in which the product is a complex machine. Rigorously exploring, conceptualizing, and prototyping the product early-on ensures that the development rides on the correct trajectory. Depending on the project complexity, there can be several iterations of the ‘engineering analysis, concept evaluation, and down selecting’ process. This can be done at the system level or, more typically, done separately for each of the major subsystems and then brought back together for a full system analysis. Each iteration goes deeper into the design details and the down select criteria is refined and made more rigorous against the product requirements. This gives clients confidence that continued engineering resources are being invested in a project that will work.
Sometimes concept exploration requires initial prototyping to evaluate feasibility. Sigma Design, in addition to having experts in the various engineering disciplines, has a full production machine shop with commercial-grade 3D printing capabilities. By utilizing this department’s conceptualization, we can experiment with a physical concept which gives another level of understanding about how the product will perform. Sigma Design also maintains an in-house assembly lab where the design team assembles benchtop prototypes to evaluate whether or not the design is on the right track in form, fit, and function. With concept through production capabilities in-house, prototypes can be rapidly iterated to explore concept feasibility. Feedback provided to the client regarding prototype performance relative to the product requirements helps the client and the design team make important decisions that influence the success of the product.
In summary, the concept exploration and selection process is valuable as it helps clients decide on the best concept to pursue early in the process. Starting development on a non-optimal concept can lead to expensive rework later in development. While clients ultimately decide which concept to pursue, they value consulting with us, as we leverage our structured concept selection process and our prototyping capabilities to provide factual feedback and input on various concept ideas.