Mechatronics

Mechatronics is a portmanteau of Mechanical and Electronics Engineering, encompassing electric motor drives, sensors, robotics and anything else where electricity is converted to (or from) mechanical energy. The –tronics suffix of the term Mechatronics refers to electronic (versus electrical) driving and control of mechanisms; or, even more fundamentally, the electronic conversion between electrical and mechanical forms of energy. Electronics Engineering is differentiated from Electrical Engineering by its association with silicon semiconductors, which are further associated with low (according to the IEC, extra-low) voltages, digital logic, integrated circuits (ICs), and . . . computers!
Twenty five years ago, Sigma Design originated as a Mechanical Engineering design firm; we have since expanded to encompass all aspects of (and disciplines required for) end-to-end product design, but Sigma Design’s Electrical Engineers do like to honor our founding spirit: making things move!
ELECTRONIC ASPECTS OF MECHANICAL MOTION
Motors and their power supply, drives, and control circuitry are important facets of Mechatronics. Simple and cost-effective AC Induction Motors, such as those used in home appliances like laundry machines, have historically been considered Electrical, although modern electronic variable-frequency inverters have allowed for speed control; DC brushed motors, brushless DC (BLDC) motors, stepper motors, servos, solenoids, or even piezoelectric actuators have always been Electronic due to the necessity of semiconductors to optimize their power supply, drive, and motion control circuits.
POWER SUPPLIES
Power supplies convert power from one voltage and/or quality to another. The design of these is considered one part of power electronics. Almost all electronic systems need several power supplies: most often, AC-to-DC and DC-to-DC converters. Some high-power motor systems will rectify AC line power to DC just so that the drive can invert it back to AC at a different frequency! We use semiconductor components such as diodes and transistors to improve the efficiency of these power supplies to minimize energy consumption, heat gain and enable battery operation. Power supplies for Mechatronic applications must generally be low impedance in order to satisfy sudden current demands. In addition, with the high energy density provided by Lithium batteries, battery–powered Mechatronics devices have also become widespread enough to include even electric cars and UAVs!
MOTOR DRIVES
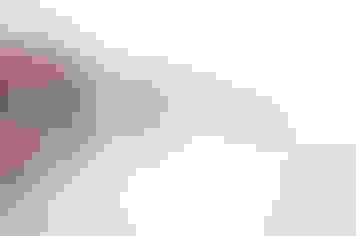
Motor drives apply power from the supplies to the motor windings with carefully controlled timing through electronic semiconductor technologies. Transistors are used (often through an H-bridge topology) to invert polarities to change DC motor direction or to invert DC into an AC waveform; diodes help protect sensitive components from flyback, voltage spikes caused by the rapid switching of motor windings, which are inductive loads. Like power supplies, motor drives fall under the domain of power electronics.
MOTION CONTROL
Finally, microcontrollers or FPGAs are programmed to provide real-time response to signals and sensor feedback to control motion through the drive circuit. Optical or Hall-effect encoders, often incorporated directly into servos, can provide absolute or relative positional feedback to ensure precision and accuracy; current sense can be utilized for “sensorless” positioning, torque monitoring, and preemptive detection of overcurrent or overheat conditions.
MECHATRONICS DESIGN CONSIDERATIONS
Since motors and other mechanical “outputs” generally require higher amounts of electric power than most other (non-electromechanical) electronic components, the design of their power supply and driving circuits can pose unique challenges: maintaining Power Integrity (PI), thermal management and Electromagnetic Compatibility (EMC).
POWER INTEGRITY
To prevent functional failure or intermittent unreliability, system voltages must be regulated within a certain tolerance: a system that allows for too much deviation from nominal can cause unpredictable behavior or even unexpected system reset or shutdown events. Ensuring a low-impedance power source for the motors is key: sufficient quality of bypass capacitance must be designed into the system in order to supply the sudden, transient current demands from a pulsing motor drive, offsetting the resistance and inductive reactance that can choke the supply and cause voltage droop.
As a consequence of any additional bulk capacitance, inrush currents when initial power is applied or when subsystems are hot-plugged can be high and must be predicted and managed during the design process to prevent transient overloading of power supplies. Many power regulation ICs will shut down when an overcurrent condition is detected, as a protection measure; excessive inrush current can cause them to go into an endless shutdown-restart cycle, preventing device functionality entirely.
Additionally, since motor windings (being coils) are inductive loads and motor speed is usually controlled through Pulse-width Modulation (PWM), each pulse or acceleration of the motor can induce a substantial back-EMF voltage spike called flyback; sensitive components must be protected from these transient overvoltage conditions.
THERMAL MANAGEMENT
Due to the higher-than-typical power levels employed in Mechatronic systems, thermal management becomes a prime design consideration: Engineers must design their systems to be as efficient as possible to avoid generating excess waste heat. Since 100% efficiency will never be achievable, modeling the heat generated by all power supply and drive subcircuits and ensuring that excess heat can be sufficiently dissipated away from the system to avoid component overheating (or causing touch hazards!) is important. Circuit designers and controls Firmware Engineers must also be careful not to allow for transient electrical shorts in the motor drive when inverting polarity.
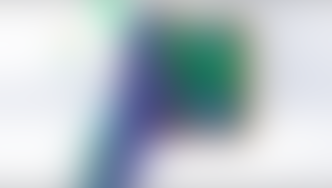
Additionally, provisioning reliable temperature feedback mechanisms to allow for damage-preemptive thermal shutdown are among many best practices for providing safe, reliable Mechatronic systems. More useful is designing effective mechanical cooling systems for thermal transfer away from heat-generating components to maximize duty cycle. Luckily, Sigma Design has a capable team of Mechanical Engineers ready to help!
ELECTROMAGNETIC COMPATIBILITY
Also due to the rapid, pulsed switching of high electric currents in motor drives, Mechatronic systems can struggle with electromagnetic compatibility (EMC). EMC encompasses how an electrical device interacts or “plays nice” with the electromagnetic world around it, and is tightly regulated worldwide by various government bodies: in the United States, the Federal Communications Commission (FCC); in the European Union, the Conformité Européenne (CE), and so forth. Since electrical devices can potentially interfere with other electrical devices and pose safety hazards, all electric products on the market must be tested for and be verified to conform to EMC regulations. Therefore, designing products to meet those requirements is an important factor in minimizing time-to-market.
In Mechatronics, conducted and unintentionally-radiated emissions are important issues to consider early on in the design process. Rapid switching of electric current can cause high-frequency voltage disturbances to be conducted back onto the power lines, which could easily violate conducted emissions standards if left unaddressed; besides working to reduce the source of noise, this back-conductance of noise is usually prevented through common- and differential-mode power filtration. Since power filtration inherently increases the impedance of the power source, consequences to Power Integrity must be carefully considered.
Alternating currents used in motor drive also generate strong magnetic fields, which can lead to radiated emissions that may interfere with other electronics (or, at least, fail EMC emissions testing). Since the generation (or reception) of magnetic fields is determined by the “loop area” of the current flow, the designer must focus on minimizing that loop area, which includes the PCB(s) as well as the motor leads. Cautious design of the drive circuitry to reduce PWM slew rate, while at odds with thermal management, can help reduce emissions. Shielding and bonding of metal components to minimize common-mode radiation caused by capacitive coupling can also be critical to prevent EMC test results that might inadvertently delay a product’s Time to Market.
CONCLUSION
Motors convert electrical into mechanical energy, but the same systems can be used to convert mechanical into electrical energy; they are then called generators. Simple generators can be used in energy harvesting applications to allow devices to function without requiring purposeful, user-initiated charging, which can be desirable in the wearables market.
In addition to electromagnetic motors, voice coils and solenoids, there are a few other ways in which electricity can be converted to mechanical motion or vice-versa. Piezoelectricity and electrostatics are some examples of these alternative technologies, but they are usually employed on smaller scales of mass or travel length, such as within Micro Electro-Mechanical Systems (MEMS) integrated circuits.