Automated Part Feeding
Our customer faced a challenge meeting production schedules due to equipment limitations and staffing constraints. Sigma Design retrofitted their equipment with automated part-loading, increasing capacity and efficiency without adding operators.
The customer’s Taperlock work cell, which included a Fanuc Robodrill α-T21iF Vertical Machining Center (VMC) and a semi-automated material handling system, required manual part loading by an operator. This system processed 23 different parts, each requiring unique machining, optical recognition, and robot programming.
The goal was to eliminate the manual single-part feeding process and enable the system to process entire totes of parts autonomously. The project required the integration of an Asyril Asycube Flexible Feeder, alongside a new part infeed system, while reusing existing equipment such as the robot, fixtures, system frame, and tooling.
The solution eliminated the need for manual part feeding and significantly increased system throughput. By retrofitting existing equipment and leveraging advanced flexible feeding technology, the customer achieved their production goals without requiring additional operators, enhancing efficiency and reducing operational costs.

The customer’s Taperlock work cell, which included a Fanuc Robodrill α-T21iF Vertical Machining Center (VMC) and a semi-automated material handling system, required manual part loading by an operator. This system processed 23 different parts, each requiring unique machining, optical recognition, and robot programming.
The goal was to eliminate the manual single-part feeding process and enable the system to process entire totes of parts autonomously. The project required the integration of an Asyril Asycube Flexible Feeder, alongside a new part infeed system, while reusing existing equipment such as the robot, fixtures, system frame, and tooling.

Sigma Design collaborated with the customer to retrofit existing components and implement new automated part-loading capabilities, improving efficiency and throughput.
Analysis & Modeling
- Acquired physical samples and 3D CAD models of all parts.
- Created a 3D CAD model of the work cell, including measured models for undocumented components.
- Imported the model into Roboguide and simulated robot paths with Fanuc to estimate cycle times.
- Developed system throughput models and cycle time estimates for each part.
System Optimization
- Refined conveyor controls to ensure reliable feeding of all 23 different parts.
- Optimized Asyril table vibration recipes for presenting pickable parts to the robot.
- Streamlined robot paths for efficient part handling.
- All these efforts delivered significantly faster cycle times compared to previous times.

Robot Programming
- Updated motion paths to accommodate new pick-and-place locations and minimize part handling time, improving efficiency.
- Fine-tuned Fanuc IR Vision software for flexible feeding, making on-site adjustments to address unique lighting conditions and ensure optimal performance.
Material Handling
- Explored various material handling options, testing them to ensure reliability across all 23 part types.
- Designed an infeed system, a hopper with a cleated-belt conveyor, and equipped it with inductive sensors for asynchronous operation.
Closed-Loop System
- Integrated the infeed conveyor, Asyril Asycube table, and machine vision into a closed-loop system. The vision system identified parts for robot pick-up, provided positional offsets, and controlled conveyor operation based on part availability.
- Evaluated and programmed the Asyril Asycube vibrating table for all 23 parts, creating and optimizing vibration profiles.
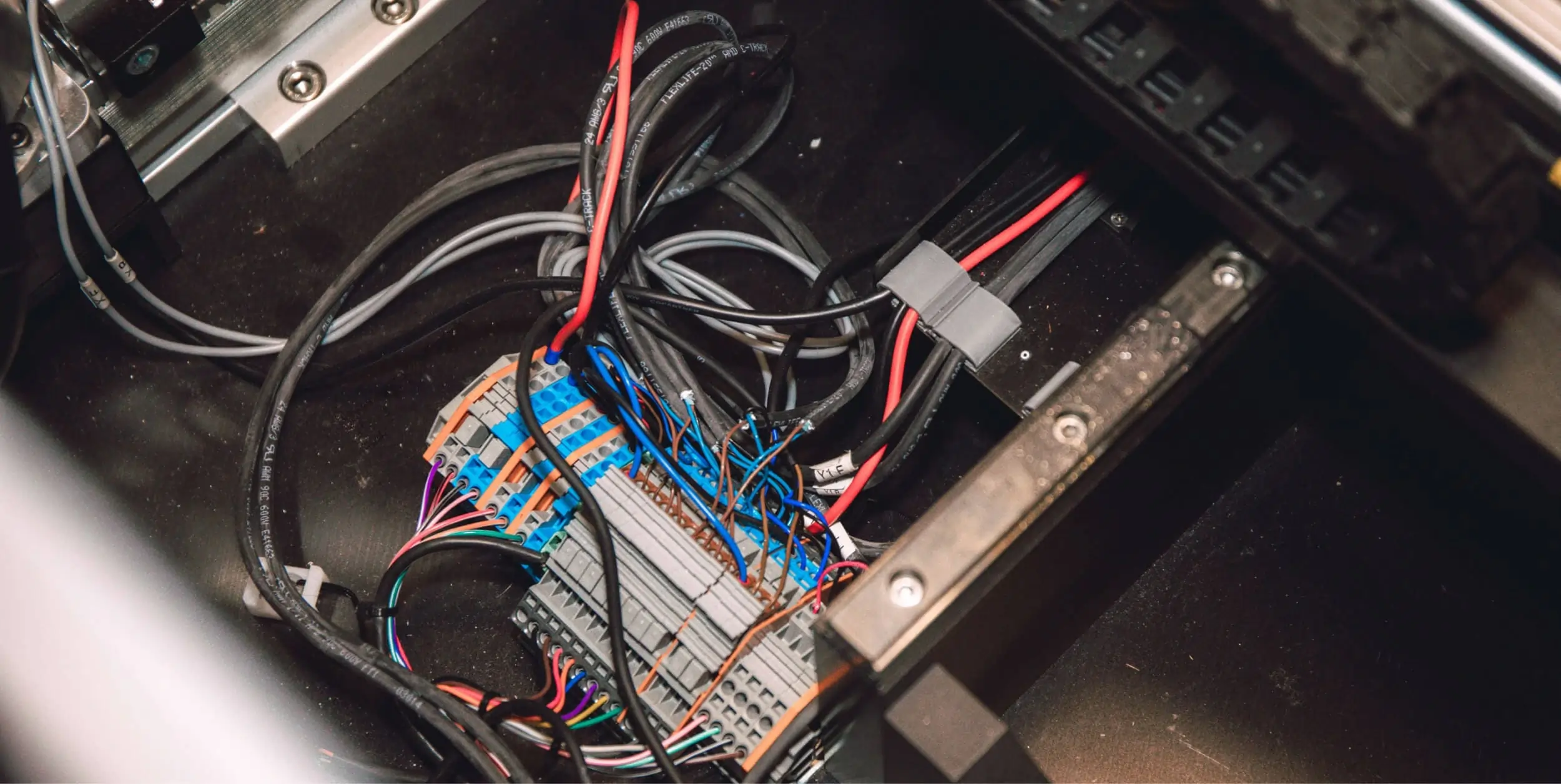