Socio Panel Lift System
An articulated and mechanized trap door that provides access for a sub-floor robot.

Introduction
The client needed an articulated and mechanized trap door that provides access for a sub-floor robot to deploy and perform a camera calibration process.
The name of this project stems from the name of the first room that housed this equipment called Socioscopy which the project entailed lifting panels from the floor. SOPLS stands for Socioscopy Panel Lift System. The acronym has become the de facto project name, although we have completed 4 different variations of this project for different facilities.
SOPLS Carousel
All About SOPLS

Problem Statement
A space containing multiple cameras is used for video capture of physically active human participants. Floor deflections of < ¼” under large human-generated dynamic loads is required. Frequent calibration of the cameras is also required, and an industrial robot is utilized for this process. When not in use, the robot is stowed below the floor. The original room incorporated a floor panel system whose removal and replacement were both manual and time consuming. When the robot is deployed, the trap door must not occlude the fields of view of any of the cameras.
A mechanized system is needed which operates in under a minute, meets the stiffness and stowing specifications, and communicates safely.
Solution
We inspected the space and integrated measurements with existing 3D models to develop a comprehensive model of the room, robot, and camera assembly. Communications protocols with the robot were determined. Design alternatives were developed, and a final design that met the requirements was fabricated, tested, integrated, and installed at the customer facility. The system has been successfully implemented in 3 different facilities in Pennsylvania and California.
Here’s How We Solved It
Analytical and FEA methods were used to design a composite welded steel and aluminum honeycomb panel structure that met the loading requirements.
Servo motors, drives, and actuators were sized and specified to safely carry the system loads.
The trap door consists of two panels, one 4-foot square, the other 4 x 6 feet joined with a hinge along their short edges. A pair of Exlar electric servo-driven linear actuators links the two panels across the hinge. The large panel is attached with a hinge mechanism to the floor structure. A second pair of actuators is connected between the large panel and the floor. Yaskawa Servomotors and Drives power and control the actuators, respectively.
The door opens like a drawbridge allowing clearance for the robot to deploy from its sub-floor stowed position. Once the robot is deployed, the door starts to fold closed at the hinge between the panels. Simultaneously, the main hinge is also closed. Using coordinated motion, the panels are guided between the support structure and into the space vacated by the robot. When required, the process is reversed to stow the robot and deploy the floor.
Both operational and system protocols are in place to provide safety to the operators and equipment. During automated use, the robot controller manages events commanding both the robot and door to move safely through their motions. Manual operation for troubleshooting and maintenance by trained personnel is available.
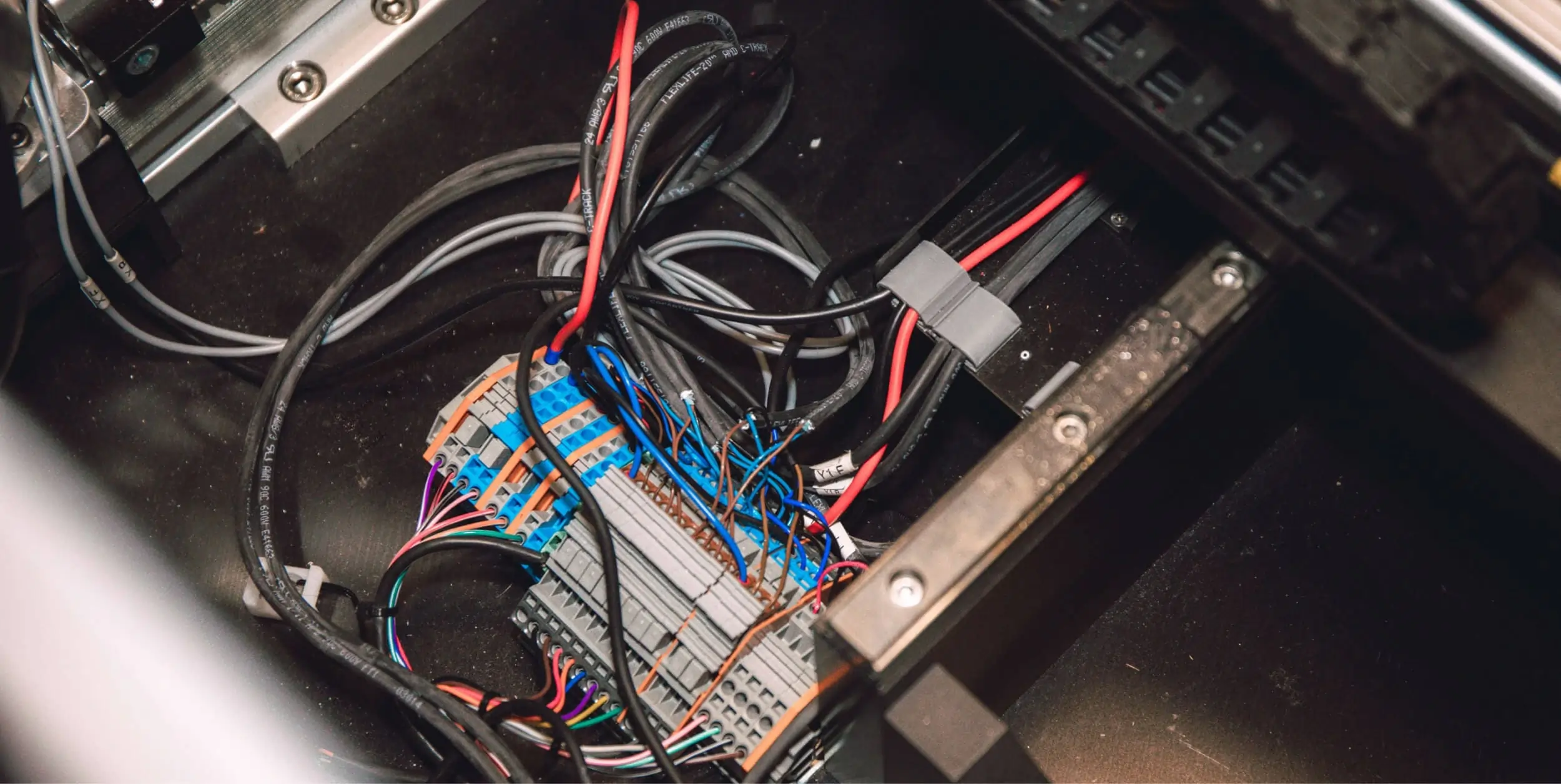